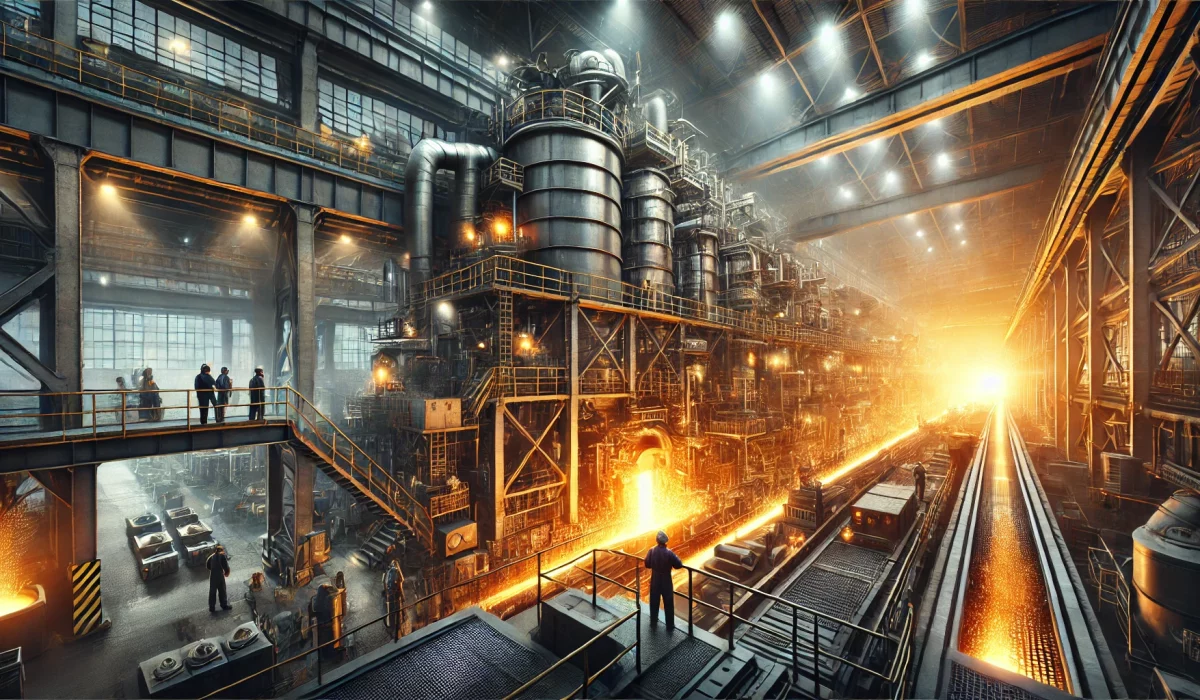
Introduction
Continuous hardening quenching furnaces are essential in the metallurgical landscape. They are known for enhancing the mechanical properties of metal components through effective heat treatment. Their applications span multiple industries, each benefiting from the precision and efficiency these furnaces provide. Below is a detailed exploration of their applications, along with temperature ranges, atmosphere control requirements, and necessary precautions.
1. Automotive Industry
Applications
- Heat treatment of gears, shafts, and critical driveline components.
- Hardening of springs used in suspensions and engine components.
Temperature Range
- Gears and Shafts: 800°C to 950°C (1472°F to 1742°F).
- Springs: 700°C to 850°C (1292°F to 1562°F).
Atmosphere Control
Controlled atmosphere (e.g., nitrogen or argon) to prevent oxidation and decarburization.
Precautions
- Ensure uniform heating to avoid warping.
- Monitor quenching medium temperature to prevent thermal shock.
2. Aerospace Industry
Applications
- Heat treatment of key components like landing gear and engine parts.
- Treatment of titanium and nickel-based superalloys.
Temperature Range
- Aircraft Components: 900°C to 1100°C (1652°F to 2012°F).
- Titanium and Superalloys: 700°C to 1000°C (1292°F to 1832°F).
Atmosphere Control
An inert gas atmosphere (argon or vacuum) is essential to prevent contamination and oxidation.
Precautions
- Use temperature profiling to ensure uniform heating.
- Implement strict monitoring of cooling rates to avoid residual stresses.
3. Tool and Die Manufacturing
Applications
- Hardening of cutting tools and moulds.
- Treatment of high-speed steel and carbide tools for enhanced longevity.
Temperature Range
- Cutting Tools: 800°C to 1200°C (1472°F to 2192°F).
- Molds and Dies: 850°C to 1050°C (1562°F to 1922°F).
Atmosphere Control
Controlled atmosphere (nitrogen or inert gas) to minimize oxidation.
Precautions
- Regularly calibrate temperature sensors.
- Monitor cooling rates to prevent cracking.
4. Construction and Heavy Equipment
Applications
Treatment of structural components and heavy machinery parts.
Temperature Range
- Structural Components: 600°C to 750°C (1112°F to 1382°F).
- Heavy Machinery Parts: 700°C to 900°C (1292°F to 1652°F).
Atmosphere Control
Generally, it is air or inert gas, depending on the material and desired properties.
Precautions
- Ensure thorough cleaning of components to avoid impurities.
- Use proper quenching media to avoid thermal gradients.
5. Oil and Gas Industry
Applications
Hardening of drilling equipment and pipeline fittings.
Temperature Range
- Drilling Equipment: 850°C to 950°C (1562°F to 1742°F).
- Pipeline Fittings: 700°C to 800°C (1292°F to 1472°F).
Atmosphere Control
Inert atmosphere to prevent oxidation, especially for high-alloy steels.
Precautions
- Conduct pre-heat treatment inspections for defects.
- Use correct quenching techniques to avoid warping.
6. Electronics and Electrical Industry
Applications
Heat treatment of connectors, switches, and magnetic components.
Temperature Range
- Connectors and Switches: 600°C to 800°C (1112°F to 1472°F).
- Magnetic Components: 750°C to 850°C (1382°F to 1562°F).
Atmosphere Control
It often requires a vacuum or inert atmosphere to maintain purity.
Precautions
- Monitor for thermal expansion to avoid damage to components.
- Ensure proper cooling rates to maintain electrical properties.
7. Medical Devices
Applications
Hardening of surgical instruments and implants.
Temperature Range
- Surgical Instruments: 800°C to 1000°C (1472°F to 1832°F).
- Implants: 700°C to 950°C (1292°F to 1742°F).
Atmosphere Control
Controlled atmosphere (inert gas or vacuum) to prevent oxidation and contamination.
Precautions
- Maintain stringent hygiene standards throughout the process.
- Conduct thorough inspections post-treatment for defects.
8. Rail and Transportation
Applications
Treatment of rail components and parts for public transportation systems.
Temperature Range
- Rail Components: 800°C to 900°C (1472°F to 1652°F).
- Vehicle Components: 700°C to 850°C (1292°F to 1562°F).
Atmosphere Control
Typically, air and inert gases may be used for high-performance materials.
Precautions
- Implement fatigue testing post-treatment to ensure performance under real-life conditions.
- Monitor for uniformity to avoid weak points.
9. Consumer Goods
Applications
Hardening of kitchenware and sporting goods.
Temperature Range
- Kitchenware: 700°C to 850°C (1292°F to 1562°F).
- Sporting Goods: 600°C to 800°C (1112°F to 1472°F).
Atmosphere Control
Air or a slightly controlled atmosphere to prevent oxidation, depending on the material.
Precautions
- Ensure proper handling and cooling to avoid distortion.
- Regularly check equipment for calibration and maintenance.
Conclusion
Continuous hardening quenching furnaces play a pivotal role in enhancing the mechanical properties of metal components across diverse industries. Manufacturers can significantly improve product reliability and performance while ensuring a safe working environment by maintaining optimal temperature ranges and controlling the atmosphere tailored to specific materials and applications.
Adherence to best practices and precautions during the heat treatment process is essential to mitigate risks and achieve desired outcomes. As industries advance and the demand for high-performance materials grows, the role of continuous hardening processes will become increasingly critical, driving innovation and technological advancements in heat treatment methodologies.
If you decide to implement it in your workplace, then ‘Precision Control’ is always the best choice. We provide the best service for Continuous hardening quenching furnaces in Dubai and Riyadh.
For more information about ‘Precons’,
♥ Do call 9840930370 or Fill out our Appointment form to get in touch!
♥ Follow our Social Media pages for recent updates. Facebook | Instagram
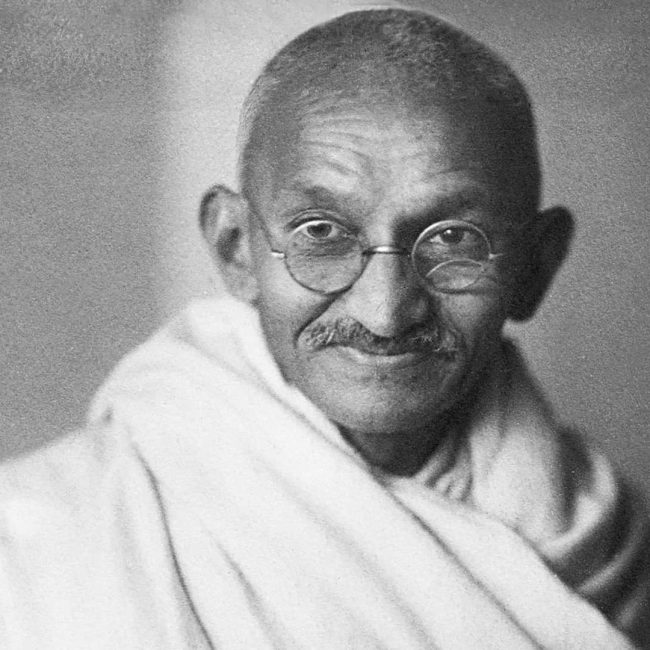
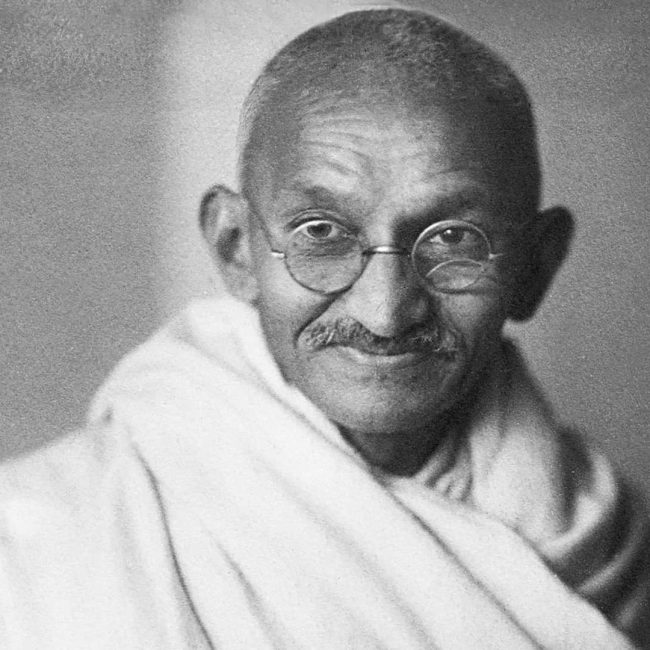