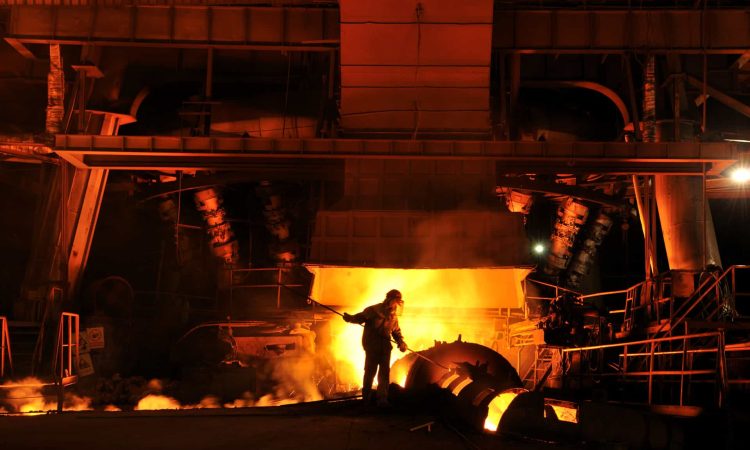
Introduction
In manufacturing, industrial furnaces serve as indispensable tools for enhancing production processes. These furnaces transform raw materials into various forms by harnessing heat energy, creating a wide range of products. From metal casting to glass manufacturing, multiple industries utilize industrial furnaces to meet the demands of modern production.
Key Components
-
Heating Chambers
These are the enclosed spaces within the furnace where the raw materials or products are placed for heating. The heating chamber’s size and shape depend on the manufacturing process’s specific requirements.
-
Burners or Heating Elements
Industrial furnaces utilize burners or heating elements to generate heat. Burners can use various fuel sources, such as natural gas, oil, or coal, while heating elements are typically electrical resistors. The choice of burner or heating element depends on factors like energy availability, cost, and the desired temperature range.
-
Insulation
Insulation is a crucial component of industrial furnaces, as it helps minimize heat loss and maintain the desired temperature within the furnace. Insulating materials such as refractory bricks, ceramic fibre blankets, or mineral wool are used to line the walls and floor of the furnace, reducing heat transfer to the surrounding environment.
-
Exhaust Systems
It generate gases and fumes during heating, and controlling their release is essential. Exhaust systems, including ventilation ducts, fans, and filters, are incorporated into the furnace to remove these byproducts safely. Proper ventilation ensures a healthy working environment and prevents the accumulation of harmful gases.
-
Temperature Sensors and Controls
Temperature sensors and controls are critical for maintaining the desired temperature within the furnace. Thermocouples and temperature sensors are strategically placed within the furnace to measure the temperature accurately. The temperature data is then sent to temperature controls, such as programmable logic controllers (PLCs) or PID controllers, which regulate the heat output of the burners or heating elements to maintain the desired temperature range.
Applications of Industrial Furnaces
-
Metal Casting and Smelting
Manufacturers extensively employ industrial furnaces in metal casting and smelting operations. They provide the necessary heat to melt metal alloys, allowing for the creation of intricate castings and the extraction of pure metals from ores.
-
Heat Treatment
Heat treatment processes like annealing, tempering, and quenching rely on industrial furnaces. These processes enhance the mechanical properties of metals, making them stronger, more durable, or more malleable as required.
-
Glass Manufacturing
It are crucial in glass manufacturing processes. By heating a mixture of raw materials, such as sand, soda ash, and limestone, in specific proportions, the furnaces facilitate the melting and shaping of glass into various forms.
-
Ceramic Production
Industrial furnaces fire clay and other raw materials in ceramic production at high temperatures. This process transforms them into durable ceramic materials used in various applications, from pottery to advanced ceramics.
-
Chemical Processes
It’s play a vital role in various chemical processes, including the production of chemicals, petroleum refining, and pharmaceutical manufacturing. These furnaces provide heat for chemical reactions, separation processes, and catalyst regeneration.
Advantages of Industrial Furnaces
-
Increased Efficiency and Productivity
It’s enable faster and more efficient production processes, increasing productivity. The controlled heating environments provided by furnaces ensure consistent quality and reduce the risk of defects or inconsistencies in the final products.
-
Precise Temperature Control
The advanced temperature control mechanisms in industrial furnaces allow for precise regulation of the heating process. This precision ensures that materials are subjected to the exact temperature required for specific manufacturing operations, resulting in optimal outcomes.
-
Versatility and Adaptability
Manufacturers can customize industrial furnaces to accommodate various materials and production requirements. They offer versatility in temperature range, atmosphere control, and heating methods, making them suitable for diverse manufacturing processes.
-
Cost Savings and Energy Efficiency
Efficient design and heat transfer mechanisms in industrial furnaces contribute to cost savings and energy efficiency. It reduce energy expenses and promote sustainable production practices by minimising heat loss and optimising fuel consumption.
Conclusion
Industrial furnaces are indispensable tools that enhance production processes across various industries. From metal casting and heat treatment to glass manufacturing and chemical processes, these furnaces provide controlled heating environments necessary for material transformation. With their precise temperature control, versatility, and energy efficiency, industrial furnaces contribute to increased productivity, cost savings, and optimized manufacturing outcomes.
If you decide to implement furnaces in your workplace, then ‘Precons furnaces’ is always the best choice.
For more information about ‘Precons’,
♥ Do call 9840930370 or Fill out our Appointment form to get in touch!
♥ Follow our Social Media pages for recent updates. Facebook | Instagram