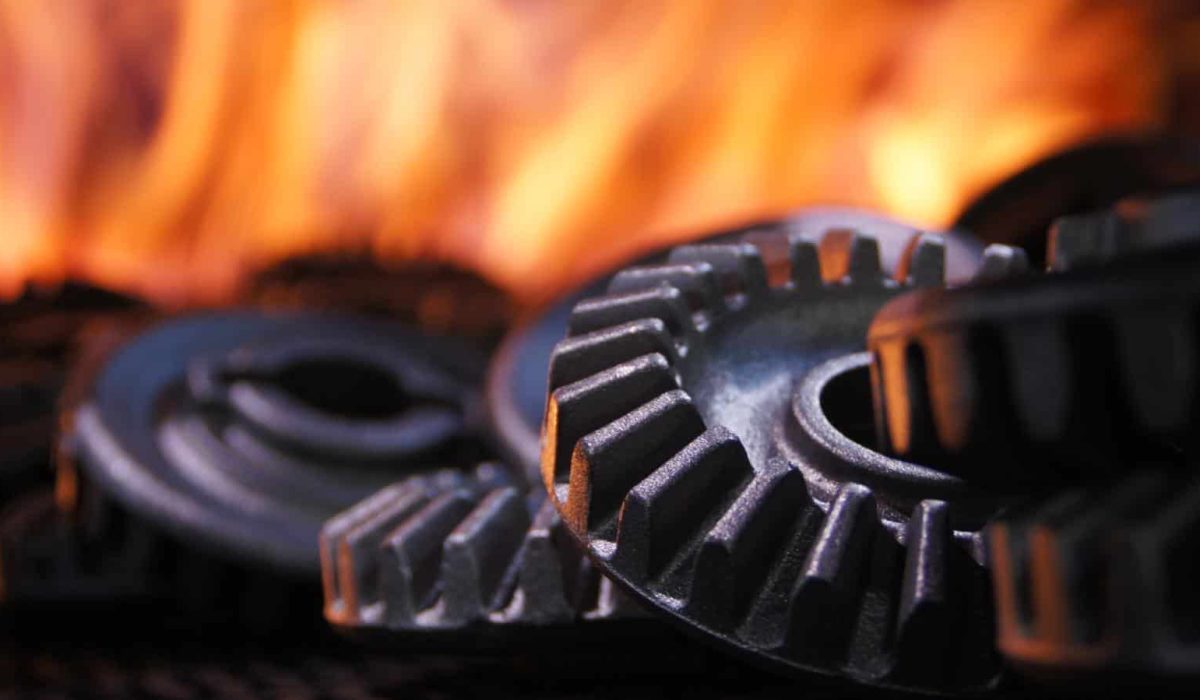
Introduction
Metallurgical furnaces, the transformative engines of modern metal processing, are profoundly evolving. This evolution is driven by the synergistic integration of sophisticated technologies, enabling unprecedented levels of precision, efficiency, and sustainability. These advancements are not merely incremental; they represent a paradigm shift, empowering industries to achieve superior product quality while minimizing environmental impact and maximizing operational efficacy.
The true importance lies in the practical application of these technologies, transforming theoretical efficiency into tangible, real-world results demonstrated by measurable outcomes. This innovation convergence is redefining the heart of advanced materials processing.
Key Technology Domains (with Quantifiable Outcomes, Practical Examples, and Enhanced Insights)
Integrated Materials Logistics and Precision Charging
• Automated conveyance systems and precision robotic charging mechanisms optimize material flow, reducing manual intervention and enhancing repeatability.
• Measurable Outcome: In modern steel mills, implementing automated charging systems has demonstrated a 25% reduction in charging time and a 5% decrease in alloy material waste, leading to a 3% improvement in final steel product consistency.
• Example: This technology transforms EAF operations, ensuring precise melt chemistries and reducing energy consumption, showcasing a shift towards streamlined, data-driven material handling.
Advanced Energy Management and Thermal Optimization
• Sophisticated heat recovery architectures, leveraging advanced heat exchangers and thermal storage, recapture and repurpose waste energy, significantly reducing operational costs and carbon footprint.
• Measurable Outcome: Aluminum remelting furnaces utilizing regenerative burners have achieved a 15% reduction in natural gas consumption and a corresponding 12% decrease in CO2 emissions. Real-time energy monitoring and predictive analytics have optimized heating cycles, resulting in a 7% reduction in overall energy expenditure.
• Example: This technology is pivotal in meeting sustainability targets within the aluminium industry, highlighting the importance of efficient thermal management.
Intelligent Process Control and Real-Time Analytics
• Supervisory Control and Data Acquisition (SCADA) and Distributed Control Systems (DCS) provide comprehensive, centralized, real-time process monitoring and control. Platform advanced sensor networks and machine learning algorithms enable predictive maintenance and adaptive process adjustments, ensuring consistent product quality and minimizing downtime.
• Measurable Outcome: In heat treatment operations, SCADA systems have reduced product defect rates by 18% and decreased downtime due to process deviations by 22%, leading to a 10% increase in production throughput.
• Example: This level of control is essential for producing high-strength components for the automotive and aerospace sectors, demonstrating the power of real-time data analysis.
Non-Destructive Evaluation and Quality Assurance
• Integrated spectroscopic and chemical analysis tools, alongside advanced non-destructive testing (NDT) methodologies such as ultrasonic and radiographic inspection, provide comprehensive quality assurance. These technologies ensure precise material composition and structural integrity, guaranteeing adherence to stringent industry standards.
• Measurable Outcome: In aerospace manufacturing, the implementation of advanced X-ray inspection has resulted in a 100% detection rate of critical internal flaws in turbine blades, preventing potential failures and ensuring a 99.9% product compliance rate.
• Example: This guarantees the safety and reliability of critical aerospace components, underscoring the necessity of meticulous quality control.
Environmentally Sustainable Operations and Emission Control
• Advanced fume extraction and filtration systems and integrated waste management protocols ensure compliance with stringent environmental regulations. Innovative byproduct recycling and treatment technologies minimize ecological impact, fostering sustainable metallurgical practices.
• Measurable Outcome: Modern copper smelters employing electrostatic precipitators and wet scrubbers have achieved a 98% reduction in particulate matter emissions and a 95% reduction in sulfur dioxide emissions, significantly improving air quality and ensuring compliance with local environmental standards.
• Example: These systems are essential for responsible copper production and showcase the industry’s commitment to environmental stewardship.
Computational Modeling and Process Simulation
• Advanced process simulation tools and computational fluid dynamics (CFD) modelling enable virtual prototyping and optimization of furnace designs and operational parameters. These simulations minimize the need for costly physical trials, accelerate development cycles, and ensure optimal performance.
• Measurable Outcome: Before constructing a new blast furnace, engineers using CFD modelling have reduced the need for physical prototype trials by 30%, leading to a 20% reduction in development time and a 5% improvement in predicted furnace efficiency.
• Example: This technology allows for faster, more efficient furnace design, highlighting the power of virtual engineering.
Real-Time Safety and Operational Integrity
• Comprehensive real-time monitoring of critical operational parameters and automated alarm and notification systems ensure a safe and reliable operating environment. Integrated safety protocols and remote diagnostic capabilities minimize risk and enhance operational continuity.
• Measurable Outcome: Furnaces equipped with thermal imaging cameras and automated alarm systems have reduced the incidence of refractory failures by 40% and prevented potential safety incidents, resulting in a 15% decrease in unplanned maintenance downtime.
• Example: This ensures a safer, more reliable operating environment, emphasizing the importance of proactive safety measures.
Future Outlook
The convergence of artificial intelligence, advanced materials science, and sustainable energy solutions defines the future of metallurgical furnaces. Predictive analytics, driven by machine learning, will enable proactive maintenance and autonomous process optimization. Integrating additive manufacturing for bespoke furnace components will enhance design flexibility and performance. Furthermore, adopting hydrogen as a clean energy source and implementing Industry 4.0 principles will drive a new era of intelligent, sustainable, and highly efficient metallurgical processes.
Emerging technologies like hyperspectral imaging, digital twins, and advanced sensor technologies will further refine process control and optimization. This continuous evolution, coupled with the demonstrable measurable outcomes, will ensure that metallurgical furnaces remain at the forefront of advanced manufacturing, driving innovation and shaping the future of materials processing. The practical application of these technologies will be the key to realizing these future benefits.
Conclusion
The strategic deployment of these synergistic technologies, with their proven, measurable outcomes, is paramount for achieving operational excellence in modern metallurgical furnaces. By embracing innovation and prioritizing sustainability, industries can unlock new levels of efficiency, quality, and environmental responsibility, ensuring a competitive edge in the global marketplace. These technologies’ quantifiable, real-world applications, combined with a forward-looking vision, truly drive the metallurgical sector’s transformative progress and advancement.
If you decide to implement high data privacy industrial furnaces in your workplace, then ‘Precons furnaces’ are always the best choice. We always provide the best installation and services.
For more information about ‘Precons Furnaces’,
♥ Do call 9840930370 or Fill out our Appointment form to get in touch!
♥ Follow our Social Media pages for recent updates. Facebook | Instagram