Corrosion Resistance
Corrosion, the stealthy thief of steel’s strength, thrives in India’s hot, humid climate with its relentless monsoons. But the steel industry has a powerful ally in its fight: the furnace. These fiery chambers, when harnessed correctly, offer a range of solutions to combat corrosion and significantly extend the lifespan of steel structures, showcasing the resilience of steel even in the harshest conditions.
Various Methods Of Corrosion Resistance
One approach involves tailoring the steel itself. Furnaces are crucial in weathering steel, a common choice for bridges and buildings. This steel undergoes a specific annealing process in the furnace, developing a protective rust layer that slows further corrosion. A real-world example is the iconic Noida Toll Bridge, constructed from weathering steel to minimize maintenance needs in the hot and humid environment.
Oil And Gas Pipelines
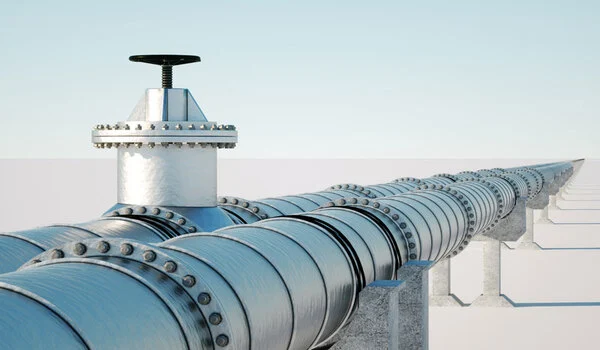
Pipelines are another battleground for corrosion. Furnaces come to the rescue with high-temperature coatings like aluminizing. This process creates a diffusion layer of aluminium on the steel surface, offering excellent resistance to oxidation and corrosion.
Especially at elevated temperatures encountered in oil and gas pipelines. For instance, Gail India Limited utilizes aluminized pipes for its cross-country gas pipelines, ensuring the long-term integrity.
Power Plants
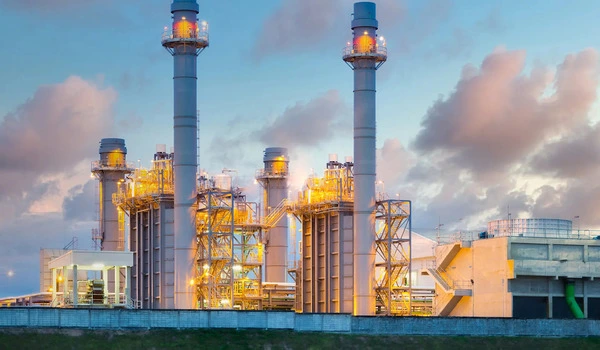
Power plants also face corrosion challenges in their high-temperature equipment. Furnaces are used for the stress relief of weldments, minimizing residual stresses that can accelerate corrosion cracking.
Additionally, furnaces can apply siliconizing coatings to these components. This creates a silicon-rich layer with exceptional resistance to high-temperature oxidation and corrosion, extending the lifespan of critical power plant equipment.
Golden Gate Bridge
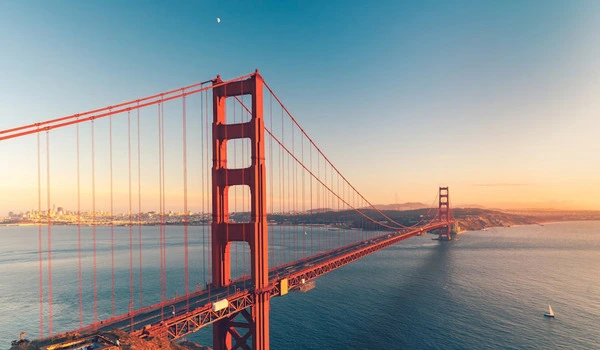
Beyond India, furnaces play a similar role globally. The Golden Gate Bridge in San Francisco, USA, endures constant exposure to fog and salt spray. To combat this, high-strength steel with a special chromium-copper content was chosen.
This steel and a special shop primer applied in a furnace-controlled environment provide excellent corrosion resistance. Additionally, the bridge undergoes regular maintenance with zinc-rich coatings for further protection.
Offshore DolWin3
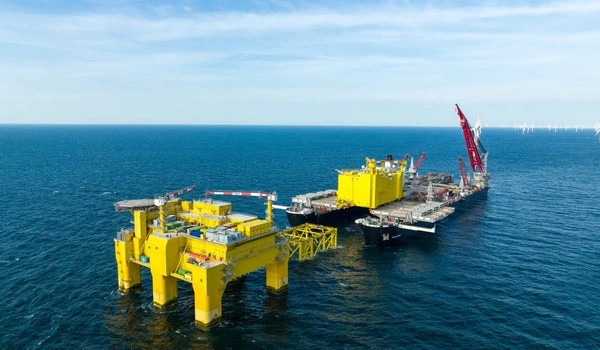
Offshore structures like oil rigs and wind turbines face a harsh combination of saltwater and wind. Here, furnaces are used for galvanizing, where a zinc coating is applied. This sacrificial layer protects the underlying steel.
The DolWin 3 wind farm in the North Sea, a massive project involving over 80 wind turbines, utilizes galvanized steel foundation jackets with cathodic protection systems for long-term performance in the harsh North Sea environment.
Conclusion
In conclusion, furnaces are not just a vital tool in the fight against corrosion but a global one. By strategically using heat treatment processes, high-temperature coatings, and stress relief, the steel industry is contributing to the creation of long-lasting, corrosion-resistant infrastructure, pipelines, and power plant equipment worldwide. This translates to significant cost savings and ensures the safety and longevity of steel structures across the globe, a testament to the collective effort in combating corrosion.
If you decide to implement high-quality industrial furnaces in your workplace, then ‘Precons furnaces’ are always the best choice. We always provide the best installation and services.
For more information about ‘Precons’,
♥ Do call 9840930370 or Fill out our Appointment form to get in touch!
♥ Follow our Social Media pages for recent updates. Facebook | Instagram